1. Scope of the coverage: |
This specification is pertinent to the application of fixed
metal oxide resistors (designated as RS). |
2 .Temperature range of the application: |
-55℃ ~ +155℃。 |
3. Type: |
Two types of fixed metal oxide resistors are
available, one is normal size and the other one is |
small size. These two types are distinguished by the color
of the coating resin. The color of the |
resin for the normal size is gray and that for the small
size is pinkish red. |
4.Marking and illustration: |
Two types of designation methods are available for metal
oxide resistors. One is black ink |
alphanumeric marking and the other one is color code marking.
The criteria of using either one of |
the marking methods depend on the size of the resistors
and customers request which is listed in |
the following: |
alphanumeric marking →1/2W、1W、2W、3W、S1W、S2W、S3W、S5W、S7W
(Fig.1) |
color code marking →1/4W、S1/2W (Fig.2) (Larger sizes are
available upon request.) |
(Fig.1) |
(Fig.2) |
Illustration of color codes: |
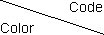 |
1-st Band
(Sig. digit) |
2-nd Band
(Sig. digit) |
3-rd Band
(Multiplier) |
4-th Band
(Tolerance) |
Black |
0 |
0 |
1 |
. |
Brown |
1 |
1 |
10 |
±1% |
Red |
2 |
2 |
100 |
±2% |
Orange |
3 |
3 |
1000 |
. |
Yellow |
4 |
4 |
10000 |
. |
Green |
5 |
5 |
100000 |
±0.5% |
Blue |
6 |
6 |
1000000 |
±0.25% |
Purple |
7 |
7 |
10000000 |
±0.1% |
Gray |
8 |
8 |
. |
±0.05% |
White |
9 |
9 |
. |
. |
Gold |
. |
. |
0.1 |
±5% |
Silver |
. |
. |
0.01 |
±10% |
|
|
5.Dimension, voltage, resistance range: listed
in the following Table |
Rated
Power
(W) |
Type |
Resistance
Range
(Ω) |
Higest
Working
Voltage
(V) |
Higest
Overload
Voltage
(V) |
2 |
J ( ±5%) |
L |
Dψ |
ι |
dψ |
1/4 |
Normal |
0.1~910K |
250 |
500 |
6±0.3 |
2.4±0.1 |
28±2 |
0.6±0.05 |
1/2 |
Small |
0.1~910K |
250 |
500 |
6±0.3 |
2.4±0.1 |
28±2 |
0.6±0.05 |
Normal |
0.1~470K |
250 |
500 |
9±0.5 |
3.0±0.5 |
30±3 |
0.6±0.05 |
1
|
Small |
0.1~470K |
350 |
600 |
9±0.5 |
3.0±0.5 |
30±3 |
0.8±0.05 |
Normal |
0.1~750K |
350 |
700 |
|
4.0±0.5 |
38±3 |
0.8±0.05 |
2 |
Small |
0.1~750K |
350 |
700 |
|
4.0±0.5 |
38±3 |
0.8±0.05 |
Normal |
0.1~330K |
350 |
700 |
|
5.5±0.5 |
38±3 |
0.8±0.05 |
3 |
Small |
0.1~330K |
350 |
700 |
|
5.5±0.5 |
38±3 |
0.8±0.05 |
Normal |
0.1~100K |
500 |
1000 |
|
8.5±0.5 |
38±3 |
0.8±0.05 |
5 |
Small |
0.1~100K |
500 |
1000 |
|
8.5±0.5 |
38±3 |
0.8±0.05 |
Small |
0.1~47K |
500 |
1000 |
For erect H
type resistor (H15、H25) |
7 |
Small |
0.1~10K |
500 |
1000 |
For erect F type resistor |
|
|
6.Coating |
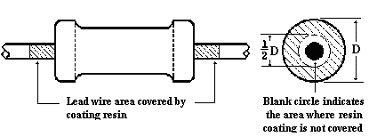 |
6.1 The body of the resistor is covered by nonflammable
silicon resin. |
6.2 The maximum length of the lead wire covered by the
resin is 2mm. |
6.3 The maximum area of the end cap which is not covered
by the resin is half of the diameter of |
the cap. |
6.4 The status of coating condition described by 6.2 and
6.3 are acceptable. |
|
7.Characteristics of electrical performance |
7.1 Rated power |
The rated power indicates the maximum power the resistor
can endure continuously when the |
ambient temperature is equal to or lower than 70℃. When
the ambient temperature is higher than |
70℃, the rated power of the resistor is determined by the
derating curve described in the following |
figure. |
|
|
7.2 Rated voltage |
The rated voltage of a resistor is either a continuous
DC voltage or an AC rms voltage which can be |
calculated by the following formula. If the calculated
rated voltage is higher than the highest |
working voltage then the highest working voltage should
be used as the rated voltage. |
P: Rated power(W) R: Nominal resistance(Ω)
E: Rated voltage(V) |
|
7.3 Insulation resistance (Ref. JIS C5202 5.6) |
Equipment: Insulation resistance tester |
The body of the resistor is wrapped around by the aluminum
foil without extending beyond the |
resistor body. Clap one electrode on the aluminum foil
and the other electrode on the lead wire. |
Apply 100V or 500V from the tester for 1 min. and the measured
resistance value should be larger |
than 1,000MW. |
|
7.4 Dielectric strength (Ref. JIS C5202 5.7) |
Equipment: Dielectric strength tester |
The body of the resistor is wrapped around by the aluminum
foil without extending beyond the |
resistor body. Clap one electrode on the aluminum foil
and the other electrode on the lead wire. |
Apply following voltage from the tester to the resistor
for 1 min. No flash-over, burning or |
breakdown should be observed. |
Type |
1/4W |
1/2W |
1W |
2W |
3W |
5W |
7W |
Normal |
250V |
250V |
350V |
350V |
500V |
---- |
---- |
Small |
---- |
250V |
350V |
350V |
350V |
500V |
---- |
Special (Erect)
|
---- |
---- |
---- |
---- |
---- |
800V |
800V |
|
|
7.5 Short time overload (SOL) (Ref. JIS C5202 5.5) |
Equipment: S.O.L. tester. |
Apply 2.5 times of rated voltage to the resistors for 5
seconds. If the applied voltage is larger than |
the voltage listed in the following table, then the voltage
in the table should be used instead. After |
the test, the sample should be stabilized at room temperature
for 30 min. before the resistance is |
measured. The change of the resistance before and after
the test should be: normal size: |
(1%+0.05Ω); small size: ±(2%+0.1Ω). |
|
Type |
1/4W |
1/2W |
1W |
2W |
3W |
5W |
7W |
Normal |
500V |
500V |
700V |
700V |
1000V |
---- |
---- |
Small |
---- |
500V |
600V |
700V |
700V |
1000V |
---- |
Special (Erect) |
---- |
---- |
---- |
---- |
---- |
1000V |
1000V |
|
|
7.6 Intermittent overload (Applicable for nominal resistance
larger than 100Ω) (Ref. JIS C5202 5.8) |
Equipment: Intermittent Table. |
Firstly put the resistor to the environment chamber at
55±2℃ and relative humidity at 20% for 24 |
hours. After that, take the resistor out and stabilize
it at room temperature for 30 min. Measure the |
resistance before the test. Put the resistor to a horizontal
position and a distance of 50mm from |
each other. Apply 4 times of rated voltage with a cycle
of 1 sec. ON and 25 sec. OFF for
|
cycles. After that, take out the resistor and let it rest
at room temperature for 30 min. and then |
measure the resistance. The acceptable % change of resistance
is: normal size: ±(2%+0.1Ω); |
small size: ±(5%+0.1Ω). The maximum applied voltage should
not exceed the value listed in the |
following Table: |
Type |
1/4W |
1/2W |
1W |
2W |
3W |
5W |
7W |
Normal |
500V |
500V |
750V |
750V |
1500V |
---- |
---- |
Small |
---- |
500V |
750V |
750V |
750V |
1500V |
---- |
Special (Erect) |
---- |
---- |
---- |
---- |
---- |
1500V |
1500V |
|
|
7.7 Flame proof (Ref. JIS C5202 7.12 3.4(2)c) |
Equipment: AC power supply |
Apply 2 times, 4 times, 8 times, 16 times and
32 times of rated voltage sequentially. The duration |
for each voltage application is 1 min.. The resistor
should not demonstrate arcing, burning or melt |
down except when the applied voltage exceeds 10
times of rated power. Under this circumstance |
of applied more than 10 times of rated power,
arcing or burning is acceptable but the duration |
should be less than 5 sec. And the height of flame
should be less than 3.5mm. The maximum |
applied voltage should not exceed 4 times of the
value listed in the following table: |
Type |
1/4W |
1/2W |
1W |
2W |
3W |
5W |
7W |
Normal |
250V |
250V |
350V |
350V |
500V |
---- |
---- |
Small |
---- |
250V |
350V |
350V |
350V |
500V |
---- |
Special (Erect) |
---- |
---- |
---- |
---- |
---- |
500V |
500V |
|
|
8.Environmental tests |
8.1 Load life test (Endurance with rated load) (Ref. JIS
C5202 7.10) |
Equipment: High temperature chamber and DC power supply |
The resistors are put in a fixture where no interference
will be allowed. Put the fixture in a 70±3℃ |
chamber and apply rated voltage with a cycle of
90 min. ON and 30 min. OFF for
hours. |
After 240, 480, 720 and 1,000 hours, the resistors are
taken out and stabilize at room temperature |
for 30 min. and then the resistance is measured. Upon each
step of resistance measurement, the |
change of the resistance should not exceed ±(5%+0.1Ω) and
the appearance should show no |
remarkable abnormality and legibility of marking. |
|
8.2 Resistance to cold (Ref. JIS C5202 7.1) |
Equipment: Constant temperature and humidity chamber |
Put the resistors to the chamber with -40±2℃, RH=90~95%
for 240±4 hours. Take them out and |
put them in room temperature for 1~4 hours then measure
the resistance. The acceptable |
change of resistance should not exceed ±(1%+0.05Ω) and
the appearance should show no |
remarkable abnormality and legibility of marking. |
|
8.3 Endurance under damp heat and load (Ref. JIS C5202
7.9) |
Equipment: Constant temperature and humidity chamber, DC
power supply |
The resistors are put in a fixture where no interference
will be allowed. Put the fixture in a 40±2℃ |
chamber with RH=90~95% and apply rated voltage with a cycle
of 90 min. ON and 30 min. OFF for |
hours. Water drops should avoid dripping
on the resistors. After 240 and 1,000 hours, the |
resistors are taken out and stabilize at room temperature
for 1 hour and then the resistance is |
measured. Upon each step of measurement, the change of
the resistance should not exceed |
±(5%+0.1Ω) and the appearance should show no remarkable
abnormality and legibility of marking. |
|
8.4 Temperature coefficient (TCR) (Ref. JIS C5202 5.2) |
Equipment: High temperature chamber |
Measure the resistance at room temperature. Put the resistor
in a chamber with the temperature of |
RT+100℃ for 30 - 45 min. to stabilize. Measure the resistance
again. Compare the resistance at |
these two temperatures with the following equation and
the acceptable value is ±350 PPM/℃. |
 |
R = Resistance at T T = RT + 100℃ Ro = Resistance at To
To =room temperature |
|
8.5 Temperature cycling (Ref. JIS C5202 7.4) |
Equipment: High temperature chamber, low temperature chamber |
Measure the resistance before the test. Put the resistor
to -55℃ chamber for 30 min. then take it |
out at room temperature for 2 to 3 min.. Put the resistor
to +155 ℃chamber for 30 min. then take it |
out at room temperature for 2 to 3 min. This completes
a cycle. Repeat the cycle 5 times. Put |
resistors at room temperature for 90 min. and then measure
the resistance. Compare the |
resistance before and after test. The acceptable change
of resistance is ±(1%+0.05Ω). The |
appearance should show no remarkable abnormality and legibility
of marking. |
|
8.6 Low temperature storage (Ref. JIS C5202 7.1) |
Equipment: Low temperature chamber |
Stabilize the resistor at room temperature for 30 min.
then measure the resistance. Put the |
resistors into the chamber and gradually lower the temperature
to -55±3℃ and maintain at that |
temperature for 24+4-0 hours. Gradually raise the temperature
of the chamber to room |
temperature and then take resistors out and stabilize at
room temperature for 1 to 2 hours. |
Measure the resistance value. The change of the resistance
before and after the test should be |
less than ±(1%+0.05Ω). The appearance should show no remarkable
abnormality and legibility of |
marking. |
|
8.7 Resistance to heat (Ref. JIS C5202 7.2) |
Equipment: High temperature chamber |
Measure the resistance at room temperature. Put the resistors
to 200℃ chamber for 2 hours. |
Take resistors out and stabilize at room temperature for
1 hour. Measure the resistance value. The |
change of the resistance before and after the test should
be less than ±(2%+0.1Ω). The |
appearance should show no remarkable abnormality and legibility
of marking. |
|
9.Mechanical performance |
9.1 Resistance to soldering heat (Ref. JIS C5202 6.4) |
Equipment: Solder bath |
Measure the resistance before the test. Immerse part of
the lead wire which is 4±0.8mm away from |
the body to the flux for 5 - 10 sec. Take the resistor
out and immerse resistors in the solder bath of |
350±10℃ for 3.5±0.5 sec.. Stabilize at room temperature
for 1 hour and then measure the |
resistance value. Compare the resistance values before
and after the test, The acceptable change |
is ±(1%+0.05Ω). |
|
9.2 Solderability (Ref. JIS C5202 6.5) |
Equipment: Solder bath |
Immerse part of the lead wire which is 4±0.8mm away from
the body to the flux for 5 - 10 sec. Take |
the resistor out and immerse resistors in the
solder bath of 245±5℃ for 3.5±0.5 sec.. Take the |
resistor out and inspect the lead wire visually. The acceptable
level is the coverage of the new |
solder to be 95%. The composition of the solder bath is
99.7% tin and 0.3% Cu. |
|
9.3 Robustness of terminals (Ref. JIS C5202 6.1) |
9.3.1 Tensile strength of termination |
Equipment: Weight gauge |
Fixed the resistor and apply axially along the lead wire
of 2.5Kg (0.8φ lead wire) or 1.0Kg (0.6φ lead |
wire) for 30 sec.. The lead wire should not break or detached
from the resistor and the change of |
the resistance should be less than ±(0.5%+0.05Ω). |
|
9.3.2 Torsional strength |
Equipment: Torsion tester |
Bend the terminal 6.4mm away from the body according to
Fig-a to 90 degree with a curvature of |
0.75mm~0.80mm. The lead wire should be clamped at a point
of 1.2mm away from the bending |
point by a fixture which can rotate 360 degree according
to Fig-b. Rotate the resistor 360 degree |
clockwise and counter clockwise for 1 cycle. The rotation
speed is 360 degree per 5 sec.. Perform |
3 cycles for the lead wire diameter of 0.8φ and 1.5 cycles
for that of 0.6φ. The terminal should not |
break down or detached from the body. The acceptable change
of resistance is ±(0.5%+0.05Ω). |
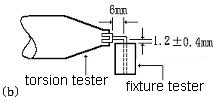 |
|